It is of vital importance that the retorts be properly installed, operated, and maintained by trained personnel.
Below context describes problems we have seen/are seeing and solutions that have been used in Innovaster retorts practical design and fabrication.
We Innovaster based in China strive for innovative solutions and improvement in retort design and manufacturing, not forgetting to deliver on cost effective retort sterilization solutions to our customers.
Here are some considerations that will help guide you through the inspectional observations of your existing steam water spray/water cascade retort.
Steam Spreader:
Are steam spreader holes clear?
Are spreaders in good condition and pointing upward?
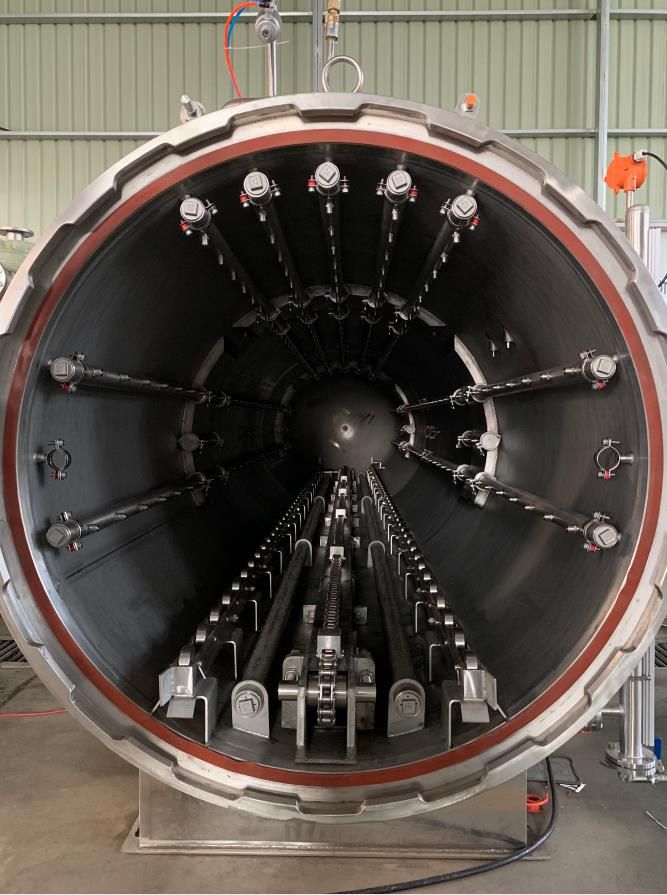
Water Drains (Recirculation Inlets):
Are drains equipped with screens to prevent clogging?
Some drains screens are designed to prevent blockage.
Water Distribution:
Are the spray nozzles/cascade holes free of debris/obstructions?
Is the filter/screen basket clear of debris/obstructions?
Is there mineral scale/buildup in the system?
Are all the nozzles in place?
Is the flow rate the same as that done in TD study?
What is the pump capacity?
Is it the same type of pump as originally installed?
Is the flow rate identified / measured as a critical factor?
Are flow rate problems identified as deviations?
Where is the flow rate meter?
Is it accurate? And how do they know?
How do they know the water level?
Is the drain valve tight sealing?
Is there a water level alarm?
Come-Up:
How is come-up documented?
Are they following the come-up procedure utilized in the Temperature Distribution study?
Are all conditions the same?
Container Size/Type?
Water Flow/Circulation Rate?
Temperature? Time?
Plumbing?
Racks? Stacking configurations?
Are come-up steps considered critical on the filing forms?
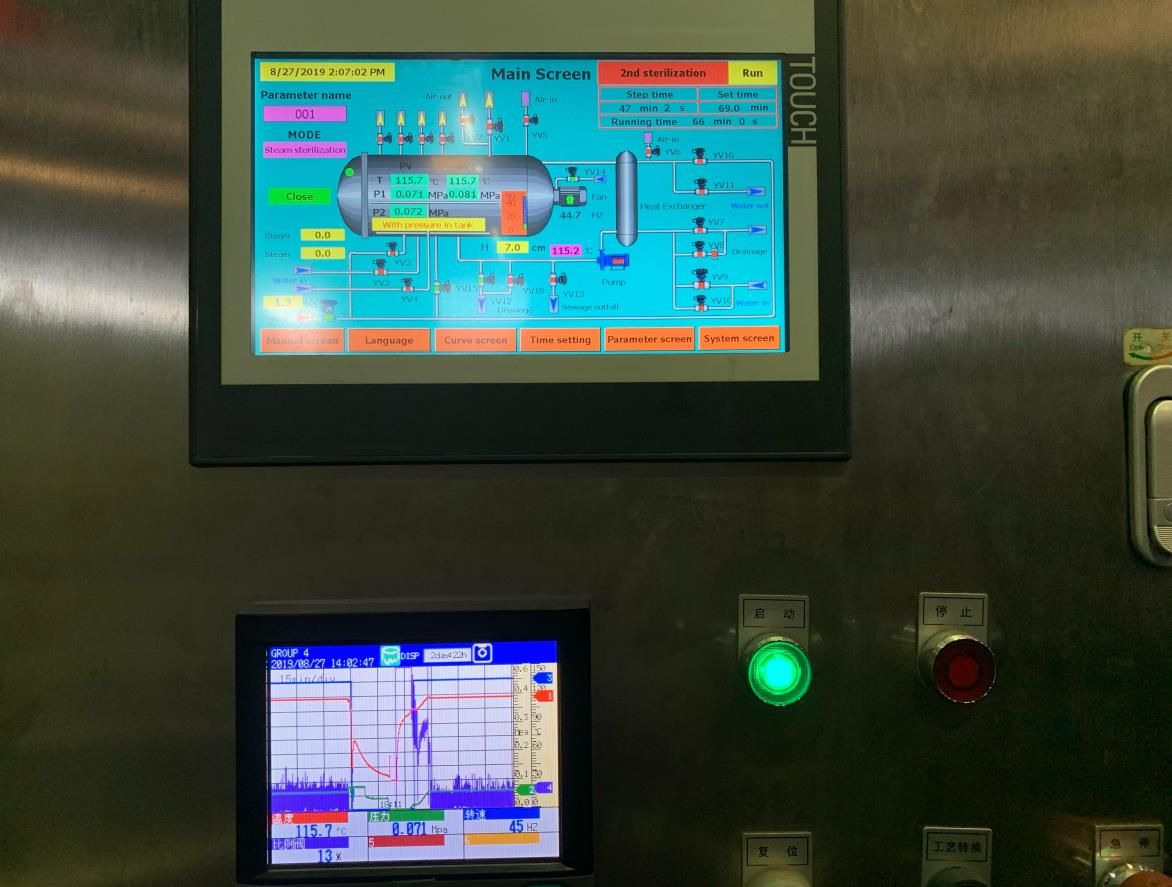
Retort Crates/Baskets and Racks:
Are they following positioning configurations from the scheduled processes?
Are racks designed for uniform heat distribution and circulation around product
containers?
Are divider/separators used to prevent shingling/mating/nesting of low profile
pouches/containers?
Is nesting/mating/shingling possible?
Was nesting/mating/shingling considered as part of the process establishment?
Any sharp points on racks?
Any collapsed racks?
Any repaired racks which could create heat distribution issues?
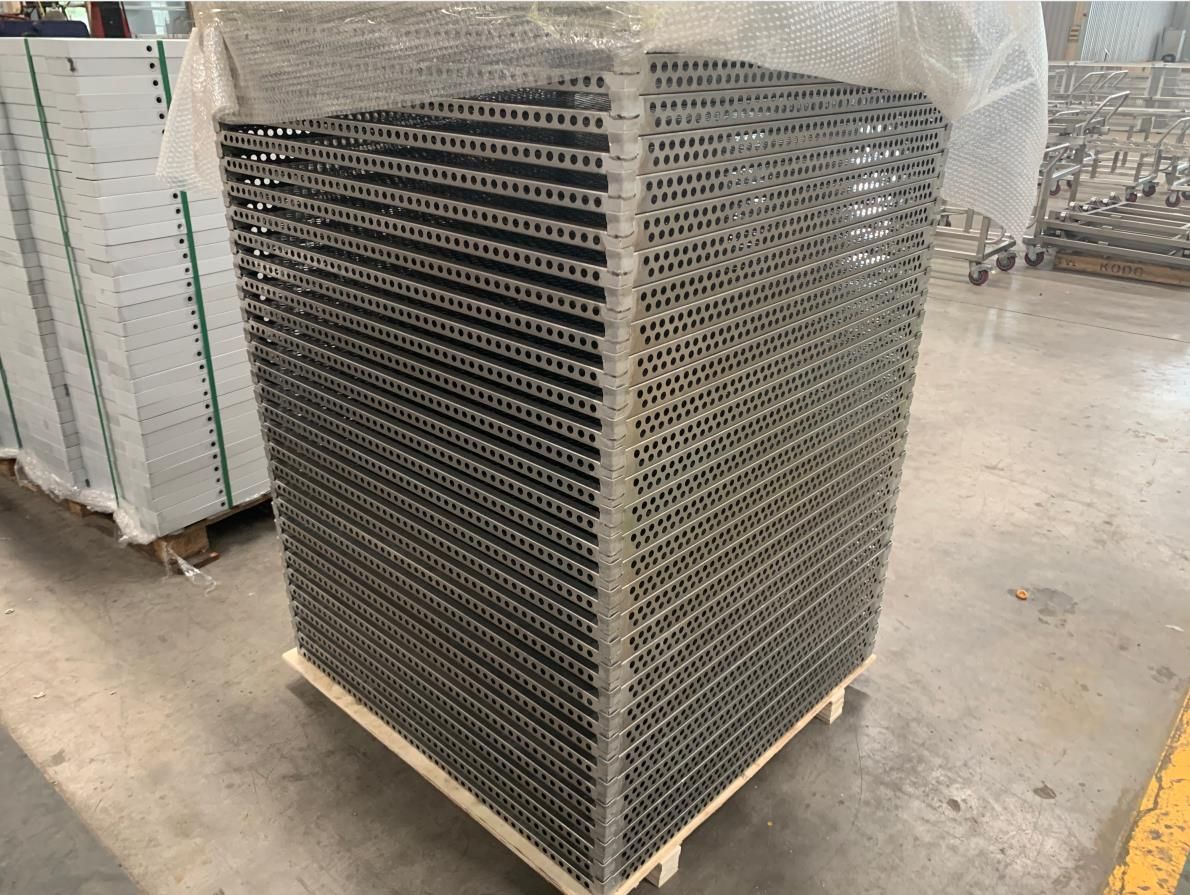
Pressure Control Pressure Control –– Air Inlets:
Does the scheduled process establish overpressure requirements?
Is overpressure monitored?
Is compressed air inlet baffled/diffused/or heated before contacting containers?
Is the compressed air inlet the cold spot?
If the air inlet is the cold spot, could a pressure control issue lead to under processing at that location (due to an unanticipated inflow of air)?
Are pressure drops considered process deviations?
How are they handled?
We hope this short context has been useful in helping you to optimise your batch retort equipment. For information on our retorts and retort room equipment, please visit our website or contact us.
Retort maintenance considerations